Economical Aspect of “Each Bar Staggering Concept” in Butt Joint Technology
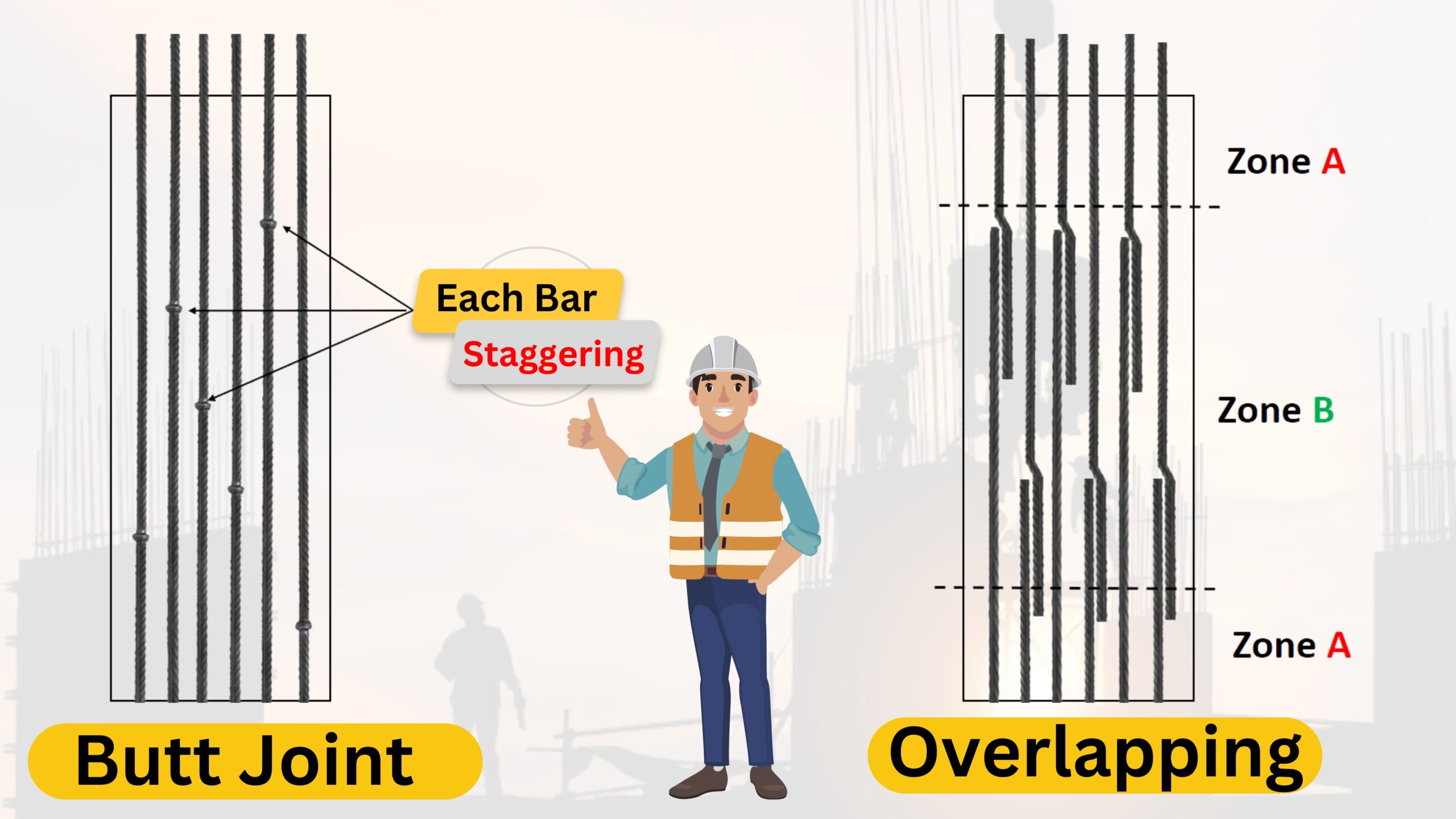
Economical Aspect of “Each Bar Staggering Concept” in Butt Joint Technology:
Introduction:
The technique of alternately placing rebar in the overlapping part of a column is referred to as “each bar staggering” in column overlapping using butt joint technology. This helps to prevent any weak points or regions of excessive stress and ensures that the weight is spread uniformly throughout the column. IS code suggesting that more than 50% of the bar should not be overlapped at a single location (IS: 456 Cl. 26.2.5 P.N. 44) because as per IS:13920 we cannot provide overlap in A-zone but with the use of butt joint technology we can stagger each and every bar and provide up to 90% of staggering using butt joint. With the use of each bar staggering concept in butt joint we can optimum utilize cutoff beam bar, TMT Unsized length and differential weight.
Here will discuss these points.
- TMT Unsized length
- Cutoff beam bar
- Differential weight
Use of TMT Unsized length:
- While manufacturing of steel rebars in mill or factories the actual length of rebar is 125m to 150m after final process. But the standard size of rebar that we required 12m length so that in mill we cut the rebar in equal size of 12m during this process some small piece of rebar like 4-5 meters are remains. These pieces are called unsized TMT rebar.
- Here we discuss about unsized length of TMT that have not acknowledge by Us but it is cost effective.
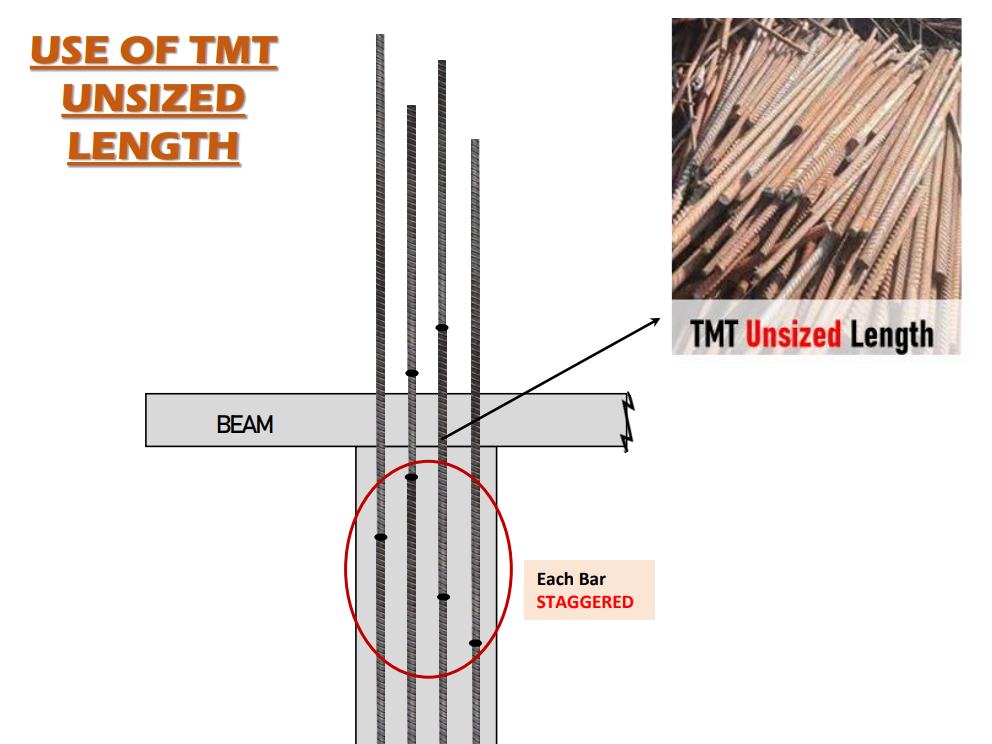
For example, fly ash which is produce in thermal power plant that is widely used in cement manufacturing. Similarly, these small pieces produce from mill that unsized TMT piece is usable for us and buy in less rate from mills. Using butt joint technique, we can effectively use the TMT unsized length so that reduces the project cost.
Use of cutoff beam bar:
- In building projects, using cutoff pieces from beams with butt joints to overlap columns is a easy and reliable approach. Through the use of the butt joint technique, the cutoff pieces produced during the cutting of beams can be repurposed and used in column.
- Using each bar staggering concept, we can effectively use cutoff pieces with the butt joint technique.
- l By the use of cutoff pieces in columns we can save project cost. There on-site, which can assist to lower the cost of the building project.
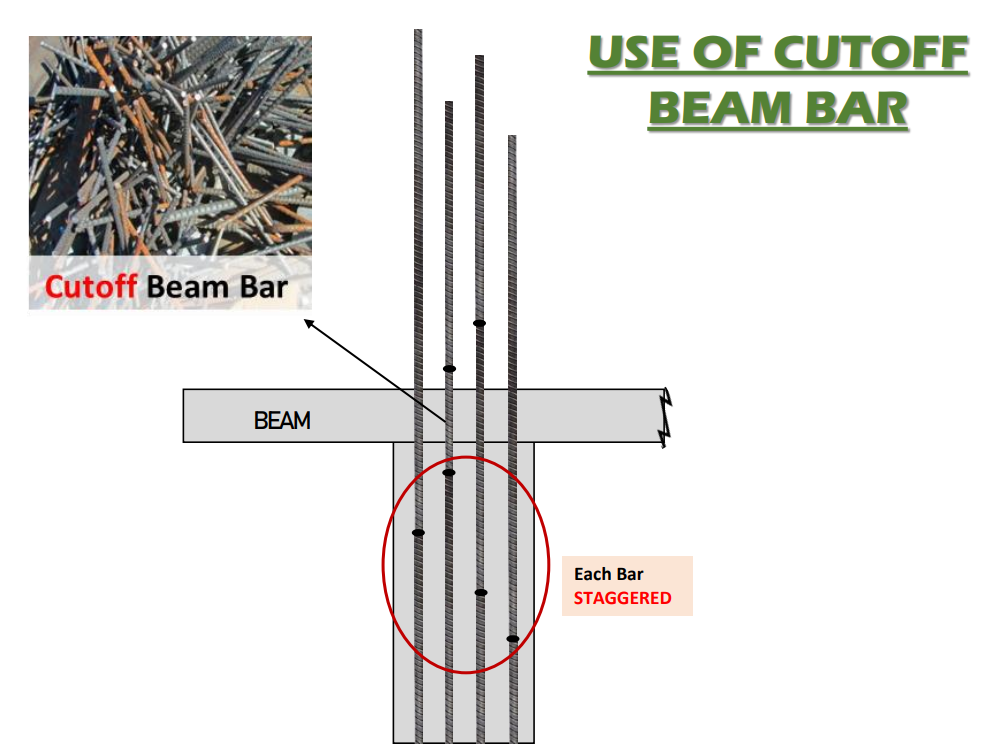
Differential weight reduced by each bar staggering:
When in column, rebar diameter is reduced in next floor in that case some rebars will extend as it is throughout the column and some rebar extent up to beam section because after that rebar diameter will be reduced (like 25mm20mm) we can join the rebar anywhere in column section using butt joint technology. By the use of each bar staggered concept in butt joint technique we can effectively use TMT unsized length and cutoff beam bar when column rebar diameter is reduced in next column. Ultimately, we can say that with the concept of each bar stagger reduces differential weight of column.
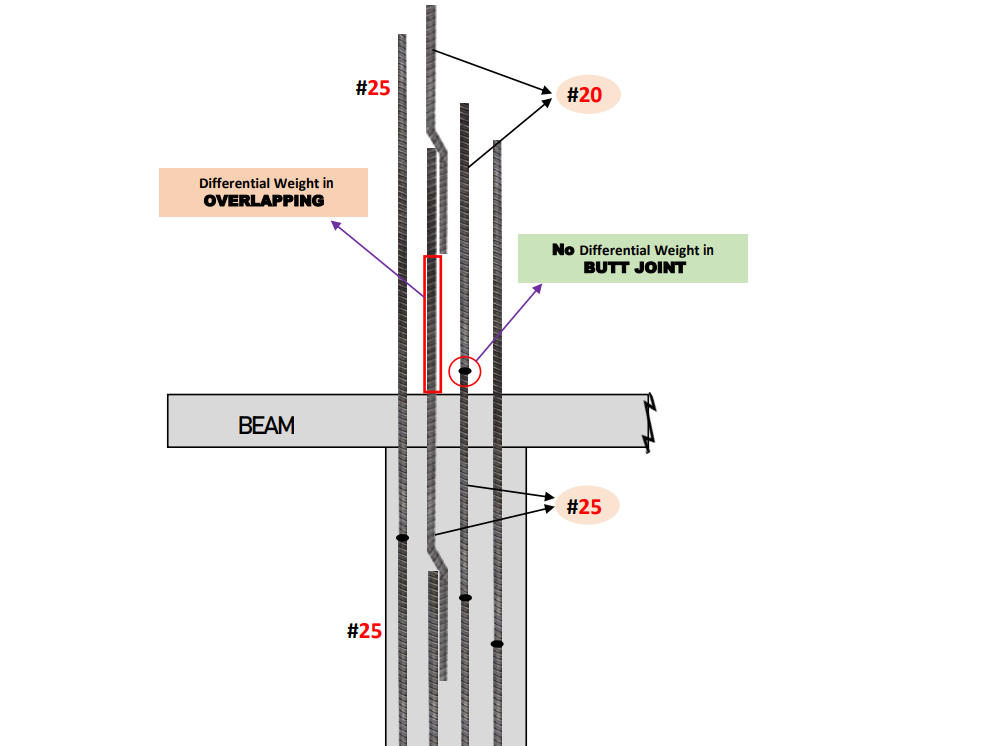
Some other advantage of staggering:
Using butt joint to “each bar stagger” the rebars in a column can have a number of financial advantages, including as lower material costs, faster construction, enhance safety.
Reduced material costs: By each bar staggering in column, the required strength and stability may be achieved with less steel using butt joint, resulting in a more economical use of resources. Savings on the materials themselves as well as the transportation of the materials may arise from this.
Faster construction: By the use of “each bar concept” butt jointing allows for quicker construction periods. This may reduce the entire construction period, so because of that our labour cost and project cost both will be reduced.
Enhanced safety: when we provide each bar stagger in column using butt joint technology then construction workers can both benefit from a stronger, more stable structure. By lowering the possibility of accidents and injuries, this may lead to savings in insurance premiums and workers’ compensation claims.